Maintaining a high level of expertise in safety management
When working with electrical equipment for railways, safety is the number one priority.
TEMS has established the TEMS Rules, which outline our unique regulations for work processes and safety. Multifaceted safety measures are in place for all of the work we do, including a framework to ensure compliance with the TEMS Rules.
We make use of a variety of venues, from safety contests at each branch to daily communication, to share information, provide safety training and improve our systems through PDCAs. As a top electrical maintenance provider for railways, we have a responsibility to maintain a high level of expertise about ensuring safety, and we are constantly striving to improve further.
TEMS Rules
The TEMS Rules have been established to clearly define our responsibilities regarding safety and work quality in our day-to-day work as a contractor. The rules are tailored to TEMS' work and contain unique regulations that we have set based on the Construction Business Act, Industrial Safety and Health Act and the regulations of the railways we serve. These rules inform everything our employees do.
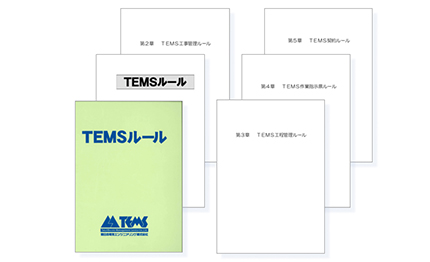
Rules are established for all levels of responsibility, including site representatives, supervising engineers, supervisors of work projects, inspection supervisors and employees of our affiliates, along with methods for checking. Five sets of rules are in place.
1. Rules for TEMS work processes
Based on preliminary meetings and on-site surveys, we plan work methodology, staffing and procedures, then predict and handle potential risks, summarizing all of this into a work safety plan to establish rules that are reflected in daily work management.
2. Rules for TEMS process management
We have established rules that dictate process from conclusion of a contract to completion of the project. Projects files are managed individually by a supervising engineer or similar supervisor who is responsible for the process as a whole.
3.Rules for TEMS safety instruction sheet management
These rules cover processes such as the creation, checking and approval of procedures and roll call for safety meeting and safety instruction sheets, chain of command, supplementary tables and other materials required for on-site safety and quality management.
4.TEMS job management rules
We organize matters according to how they must be considered during work and reflect this in daily operations.
5.Rules for TEMS subcontractor management
These rules include instruction matters concerning our safety and health education, industrial accident prevention council, safety meeting and construction safety plan meeting for our business partner.
The TEMS Safety Pyramid
These are the basic principles for carrying out work safely. The TEMS Safety Pyramid defines our framework for compliance with the TEMS Rules as an organization and the rules and responsibilities at each level.
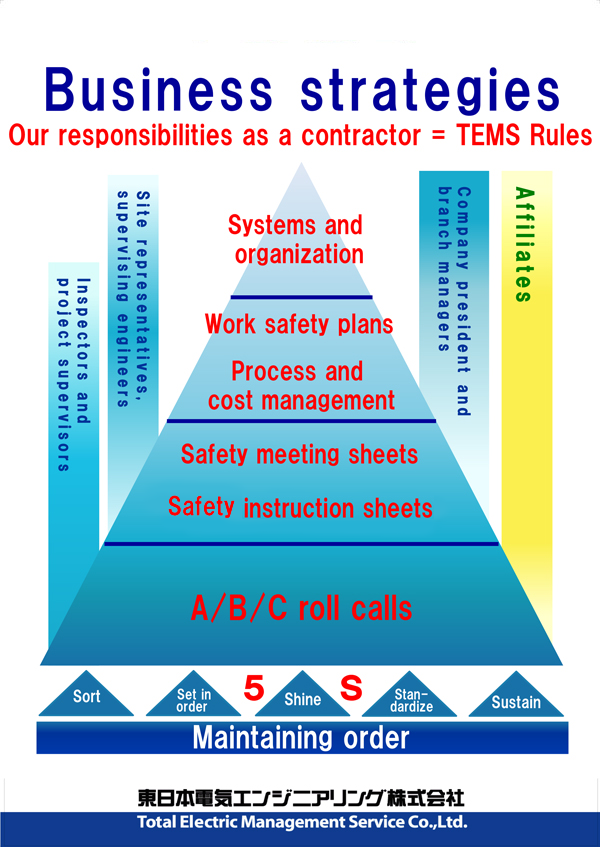
We use the 5S to maintain order in our workplaces. This is the foundation for compliance with the TEMS Rules throughout our organizations.
Everyone does their part in ensuring thorough compliance: the company president and branch managers oversee systems, organizations and contracts, site representatives and supervising engineers create work safety plans and manage processes and costs and inspectors and project supervisors perform roll calls and carry out projects based on safety meeting sheets and job instruction sheets.
Work Safety Policy
This policy is used to make sure all employees remain aware of compliance with the TEMS Rules on a day-to-day basis.
Work Safety Policy
Compliance with the TEMS Rules is how we gain customers' trust
- ・A work safety plan is always created.
- ・Safety meeting and safety instruction sheets are created correctly and checked by a site representative.
- ・Proper instructions are given during projects.
- ・Work is stopped if a rule is violated while working.
- ・Changes in the nature of work or personnel are approved by a site representative.